Computational fluid dynamics (CFD) heat transfer modeling holds significance in blast freezing due to the critical need for rapid and uniform cooling. Colmac Coil uses CFD Modeling to accurately predict the performance of the industrial refrigeration evaporator design. There are several advantages to using CFD analysis to design the optimal industrial refrigeration evaporator for new build or retrofit blast freezing, food processing or cold storage facilities:
Optimized Airflow and Equipment Placement:
Air Distribution: CFD modeling helps determine the ideal airflow patterns and distribution to achieve uniform cooling of the product throughout the storage space.
Scenario Simulation: Allows for simulations of different freezing conditions, product loads, or equipment variations to optimize the blast freezing process for different scenarios.
Placement of Equipment: CFD analysis aids in positioning refrigeration units and fans optimally to maximize efficiency and speed of freezing.
Appropriate Equipment Sizing: Models assist in selecting the right-sized equipment for blast freezing, ensuring it can handle the required cooling rates efficiently.
Time and Energy Efficiency:
Reduced Freezing Time: CFD Modeling assists in determining the optimal conditions (temperature, airflow rates) required to achieve rapid freezing while maintaining product quality.
Energy Optimization: By optimizing parameters, it reduces the energy consumption during the freezing process, minimizing operational costs. Through a CFD analysis of the blast freezer room, Colmac Coil designed and provided a reversing airflow blast freezer coil to J&D Refrigerated Services that reduced blast cell cycle time from 48hrs to 38hrs. Read the case study to learn more.
Product Quality Preservation:
Uniform Cooling: CFD modeling ensures consistent temperatures throughout the products, preventing ice crystal formation or uneven freezing that could compromise product quality.
Preserving Texture and Nutritional Value: Rapid freezing, improved by accurate modeling, helps retain the texture, taste, and nutritional value of the frozen products.
Quality Control: Predictive models help in maintaining consistent freezing conditions, ensuring product safety and quality.
Defrost Cycle Efficiency:
CFD (Computational Fluid Dynamics) analysis aids in optimizing defrost efficiency for industrial refrigeration evaporators through detailed simulations of airflow, heat transfer, and moisture distribution within the system.
Figure 2: Heating and cooling effects modeled for an A+Series® A+M Air Cooler with a return air defrost hood and air discharge sock |
Heat Transfer Analysis: CFD analysis provides insights into heat transfer mechanisms within the evaporator coil, including conduction, convection, and radiation. Engineers can evaluate how efficiently heat is transferred from the surrounding air to the coil surface, which influences the rate of frost accumulation and the effectiveness of the defrost cycle. Design options to improve the defrost efficiency of the industrial refrigeration evaporator can also be modeled, such as: Return air defrost hoods, louvers, air discharge duct socks, and more.
Optimizing Defrost Strategies: By simulating different defrost scenarios, engineers can evaluate the effectiveness of each method in removing frost from the coil surface. CFD analysis helps in determining the optimal timing, duration, and sequence of defrost cycles to minimize energy consumption and downtime while ensuring complete frost removal.
Compliance and Quality Assurance:
Meeting Standards: CFD models aid in ensuring compliance with industry standards and regulations regarding blast freezing temperatures and times for various products.
Identifying Potential Issues: CFD Models can predict potential issues with equipment or freezing conditions, allowing for preventive maintenance to avoid downtime.
Data for Innovation: Modeling provides valuable data that can be used for ongoing research and development to improve blast freezing technologies and methodologies.
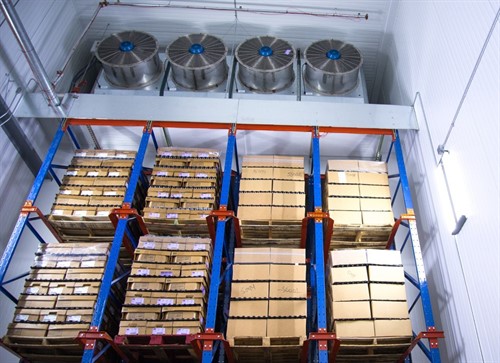 |
Figure 3: Colmac Coil Blast Cooler that was designed with the aid of CFD analysis, in a blast freezer room |
In blast freezing and other industrial refrigeration projects, where rapid and uniform cooling is paramount, heat transfer modeling becomes indispensable for achieving optimal freezing conditions, ensuring product quality, energy efficiency, and compliance with industry standards.
Sources:
Eric Alar, P.E., “Optimizing Airflow in Spiral Blast Freezers” The University of Wisconsin Madison, August 2023, https://irc.wisc.edu/helpers/file.php?ID=573
Mingkan Zhang, “A study on computational fluid dynamics modeling of a refrigerated container for COVID-19 vaccine distribution with experimental validation” Buildings and Transportation Science Division, Oak Ridge National Laboratory, One Bethel Valley Road, Oak Ridge, TN 37830, USA, https://www.ncbi.nlm.nih.gov/pmc/articles/PMC8580812/